EQUIPMENT SUPPLIED TO HOSPITAL in Oderzo (TV) Italy
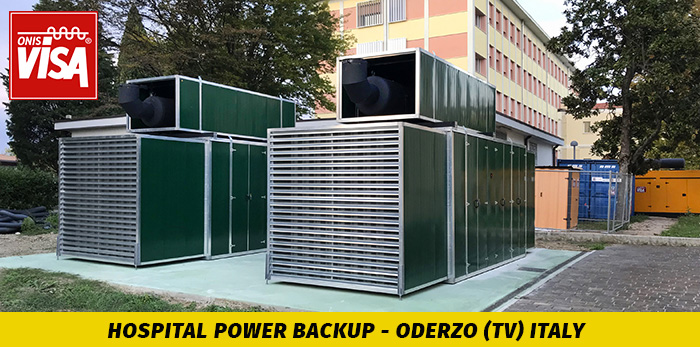
Powering life support machines: a power cut in health facilities implies very high risks with potentially lethal consequences. In order for this not to happen, it is necessary to design emergency power systems in order to minimise the risk of power failures: in this context, emergency generating sets play a fundamental role in guaranteeing a continuous and reliable power supply.
CASE HISTORY
DATA | DESCRIPTION |
---|---|
Project: | HOSPITAL INSTALLATION |
Location: | 31046 Oderzo (TV), Italy |
Power required: | 1.60 MVA (P.R.P) |
Power installed: | 1.60 MVA (P.R.P) |
Generator sets: | 2 x P 805U special version |
Dimensions: | 2300 x 6900 x 3270 mm (W x L x H) |
Purpose:
The project originally envisaged a single 1400 kVA machine but, given the need to guarantee maximum efficiency and reliability, our technicians proposed a totally redundant system, consisting of 2 800kVA generators in a special version, with parallel function and quick start procedure to ensure activation of both units within 15 seconds of the power failure, as per legislation in force relating to this type of application (ref. ISO 8528-12).
Special configuration:
Given the critical nature of the application, the machines are equipped with a total redundancy system, with parallel operation and quick start system.
To ensure maximum reliability, the special application also provides a short parallel for when electricity is resumed, to avoid a re-entry black-out during the changeover phase, implemented by means of the InteliMains board on the hospital’s distribution panel. The short parallel with the mains also provides for the possibility of performing load tests on the machines without interrupting the load.
The other special features of the system are: maximum reduction of residual vibrations and low noise levels.
Technical specifications:
Both generating sets are fitted with a Perkins model 4006-23TAG3A engine, Stamford model HCI634G alternator, IN-SYNC control panel and InteliMains mains management board.
Objectives:
The most relevant aspect of the project is the guaranteed redundancy level. The two machines have been designed to help one another: in the event of a malfunction of either one, the generating set is able to intervene by taking the most critical load.
Each machine is equipped with a double electric starter motor, a double battery pack and a double battery charger.
The two generating sets are equipped with double Comap InteliGen-NTC-BB control units and InteliVision5 display, in redundancy with automatic switching between the two controllers. The switch between the controllers, from the Master board to the Slave board, can also occur during operation in parallel.
The InteliMains board for mains control and changeover control has also been envisaged in redundant mode, with power supply from DC-UPS power supply units, which are also redundant.
Monitoring and control system:
HOSPITAL BMS INTEGRATED MONITORING
The boards controlling the generating sets and mains are equipped with Ethernet and RS485 communication ports for data communication via the Modbus protocol, allowing them to be integrated into the hospital’s BMS (building management system).
REMOTE MONITORING THROUGH GPRS
The machines have also been equipped with a GPRS InternetBridge modem with an active data sim, for monitoring the generating sets and the mains remotely via the OnisVisaWebsupervisor web platform, which allows the customer to monitor in real time the main parameters and alarms, geolocation of the generating set through GPS positioning, display the graphic trends to verify the temporal trend of the main parameters, and display periodic reports of the most important statistical data.
Technical diagnostics service:
The generating sets supplied to the hospital also feature the exclusive SupervisorPlus active supervision service provided by the Visa SPA service department, which intervenes remotely, if necessary, advising on solutions and planning interventions, before they become critical.
Refuelling system:
The fuel tank mounted on both machines has a 400 L capacity, with automatic filling pumps on the machine connected to an additional 9000 litre storage tank with double dip tube, to guarantee an operating autonomy at full load exceeding the 24 hours set by the legislation in force (ref. ISO 8528-12).
Vibration reduction:
Another important aspect requested by the customer was the maximum reduction of residual vibrations that could have been transmitted to the church in front of the system. For this purpose, the technical team has developed a system consisting of anti-seismic anti-vibration spring mounts placed between the baseframe of the machines and the supporting platform.
Soundproofing:
With regard to soundproofing, in order to be able to ensure the noise level indicated in the specification equal to 67 dbA at 7 m, a tailor-made solution was developed involving a bell-shaped canopy and residential silencer with high noise reduction coefficient.
Other special aspects:
The machines have been supplied with a special RAL6005 colour featuring an enclosure for the silencers, to be integrated in a dedicated green area to minimise the environmental impact.